Nous allons maintenant passer à la partie tansmission, enfin ce qui va faire avancer notre loco .
Je commence par l'usinage des pignons ,ce sont des 70 dents au module de 1,5.
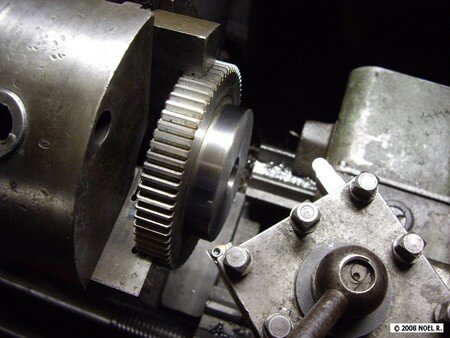
Il faut les réduire en épaisseur pour la circonstance .
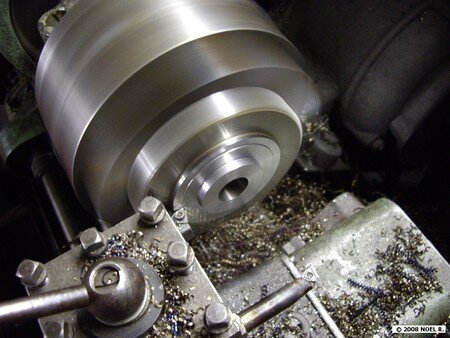
Tournage de l'épaulement de diamètre 39.5mm longueur 8 mm.
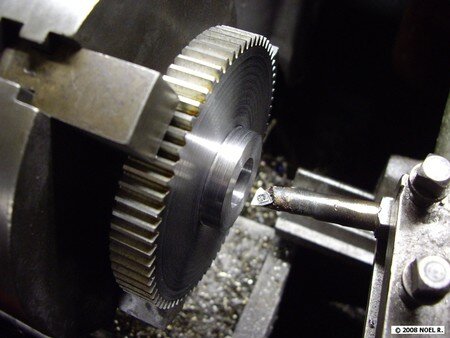
Alésage à 20H7.
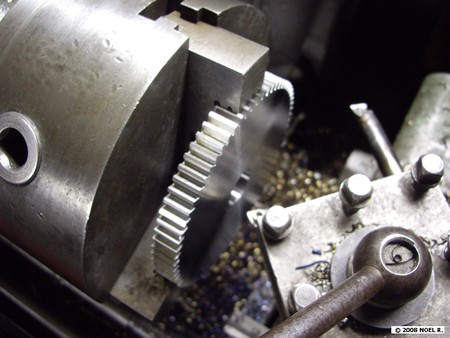
Reprise de l'autre côté pour amener l'épaisseur du pignon à 12mm.
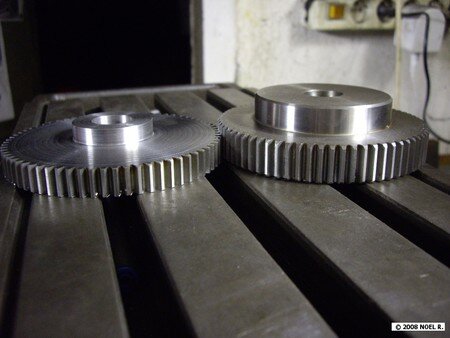
Voici un pignon modifié et un autre d'usine .
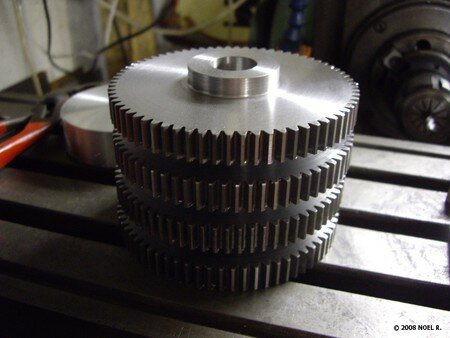
Bon maintanant il faut jouer au dentiste et ébavurer toutes les dents .
Les Moteurs
Je vais utiliser des moteurs 12V à courant continu de récupération qu'il faut modifier pour les adapter à la transmission des bogies.
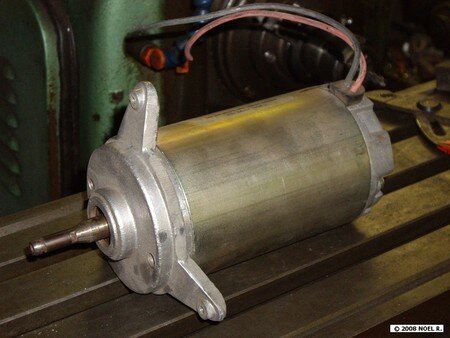
Ce moteur va subir une transformation pour vivre une nouvelle vie .
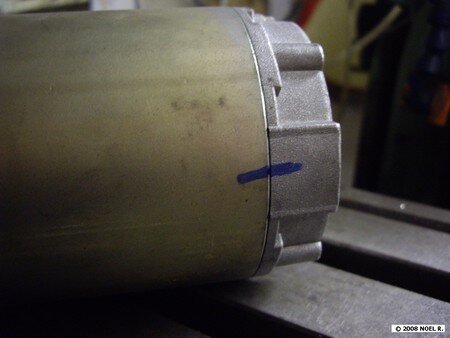
Avant de commencer on fait des marques pour s'y retrouver une fois que tout sera en vrac sur l'établi .
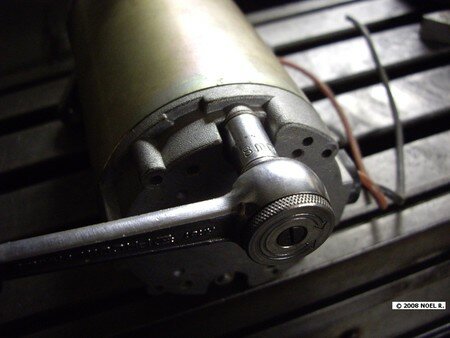
Le tout est bloqué par deux écrous M5 vissés sur les tirands qui relient les deux flasques .
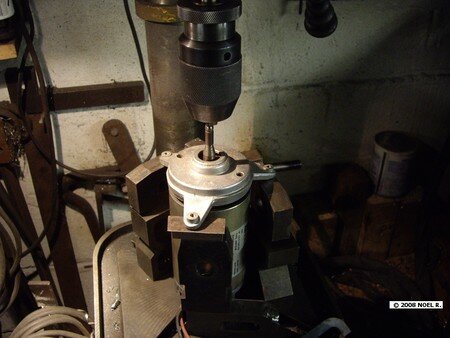
Le rotor est démonté du flasque avant en utilisant la perçeuse à colone comme presse .Le roulement avant est monté serré sur l'arbre et dans le flasque , le roulement arrière quand à lui est monté serré sur l'arbre et glissant juste dans le flasque .
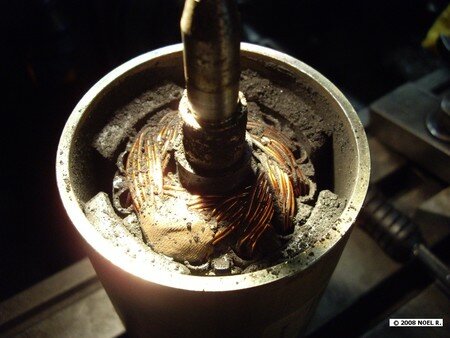
Ces moteurs sont mis au rebut car ils sont bloqués par la poussière de charbon , la preuve en est ! Sacré chantier là dedans.
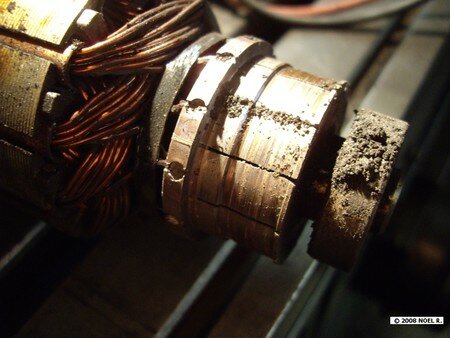
Un bon coups de soufflette et tout sera bien propre .
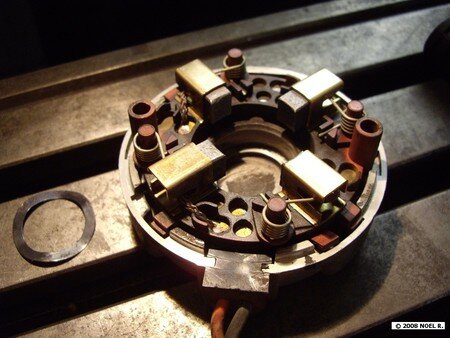
Voici la partie distribution du courant avec les charbons .La rondelle ondulée sert à compenser les variations de longueur du rotor due à sa dilatation quand il s'échauffe , c'est pour cela que le roulement arrière est monté glissant dans son logement .
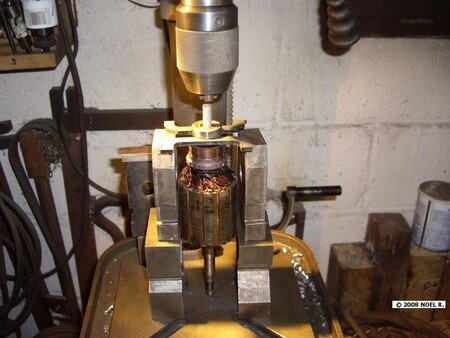
Le roulement est chassé à la presse , il ne faut pas frapper sur l'arbre pour chasser un roulement au risque de faire glisser le rotor sur son axe avec les ondes de choc et là le moteur est mort .
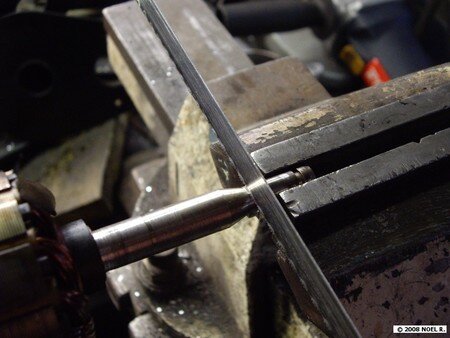
Le bout de l'axe est scié pour retirer une partie qui ne sert à rien et augmente inutilement le porte à faux lors du tournage .
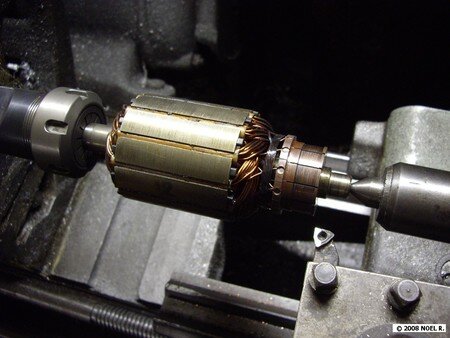
Le collecteur est un peu usé et il va être rafraîchi .
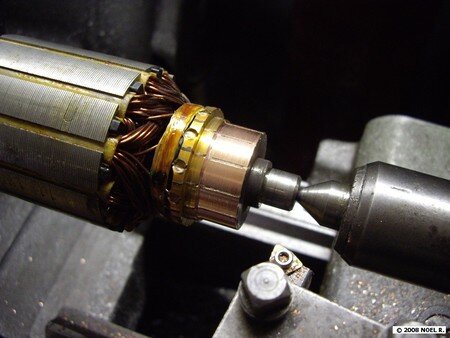
Le voici comme neuf .
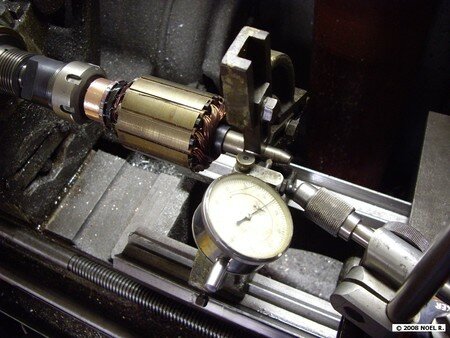
Il faut faire un nouveau centre à cette partie de l'axe , pour cela il faut utiliser la lunette fixe que l'on règle avec la procédure habituelle : la pièce est montée sans faux rond au comparateur puis les touches de la lunettes sont appliquées sans faire bouger la pièce .
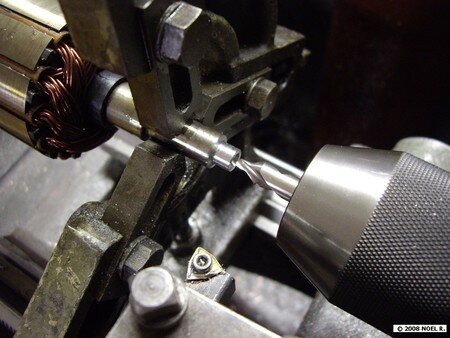
Tournage d'un petit épaulement de diamètre 7,5 mm et perçage du centre .
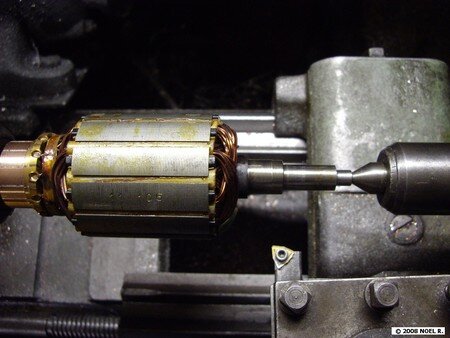
Le rotor est monté en mixte entre une pince de 12 mm et ce nouveau centre .

La portée de diamères 12 mm+0-0.01 est usinée de façon à avoir un entraxe entre les deux roulements de 119 mm .
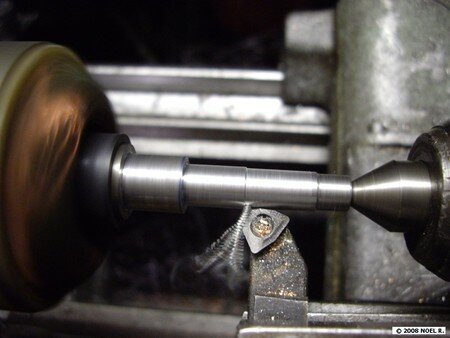
La portée du petit pignon est réalisée à un diamètre de 8h7.
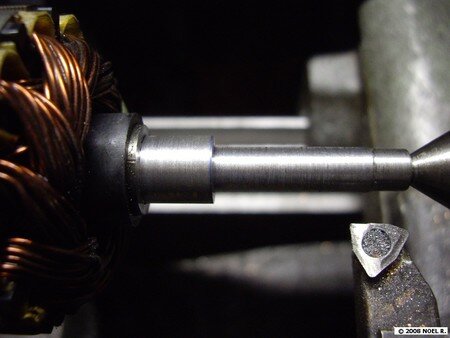
On peu voir à quoi servait le petit dégagement de diamètre 7,5 mm à droite , c'était pour le passage de l'outil au niveau de la contre-pointe .
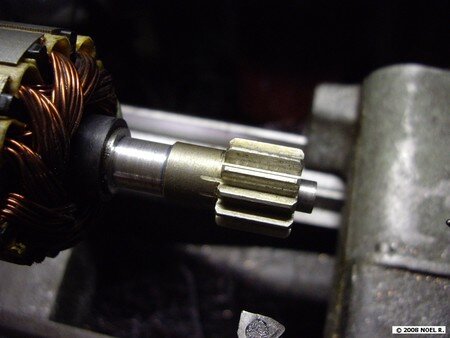
Essai de montage du pignon de 12 dents , il est encore dans sa version d'usine avec un épaulement .
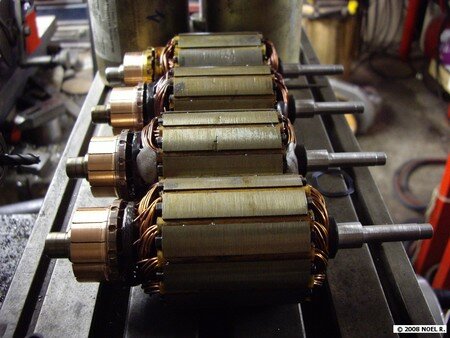
Les quatre rotors sont finis .
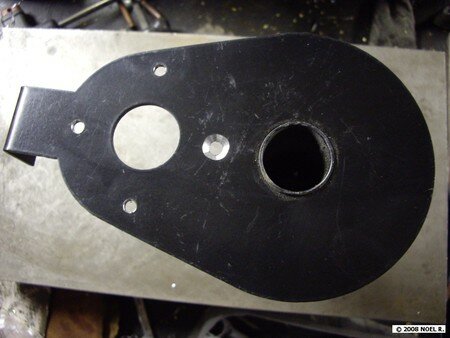
La pièce maitresse du réducteur provient des GP38 de Jacques , merci pour ta contribution .
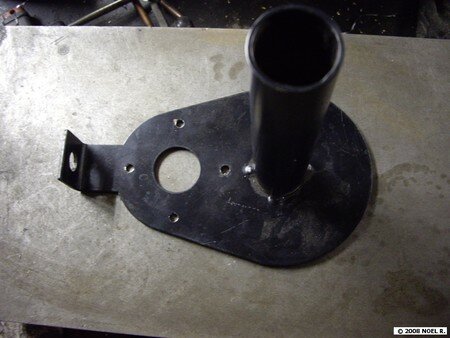
J'ai refais des trous pour la fixation du moteur , avec quatre vis il ne va pas se sauver , j'ai toujours peur que cela ne tienne pas alors qu'une vis aurai sûrement suffit !
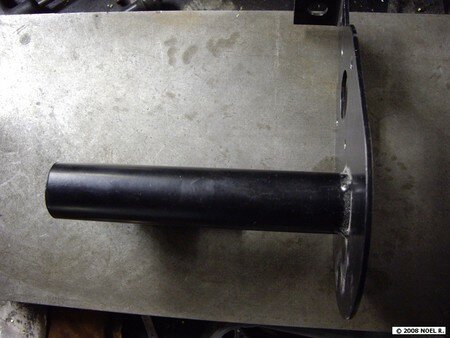
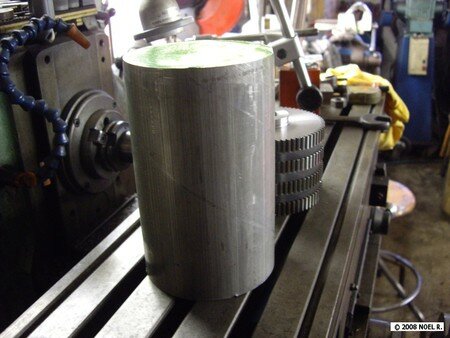
Les flasques avant sont fait dans du rond de duraluminium que j'ai trouvé sur le célèbre site de vente aux enchères , on y trouve vraiment de tout , il suffit d'être patient.
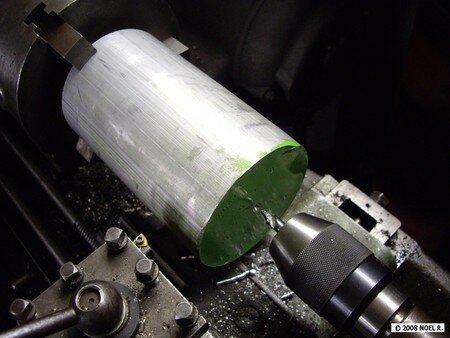
Centrage pour usiner en mixte vu le porte-à-faux.
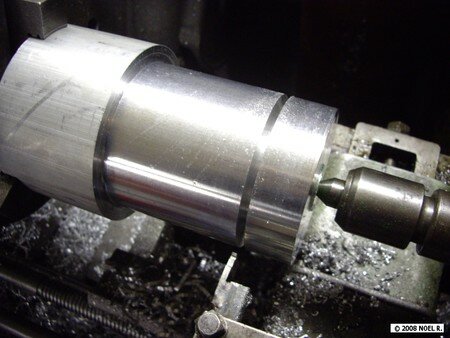
Tournage au diamètre 82mm puis tronçonnage des galettes .
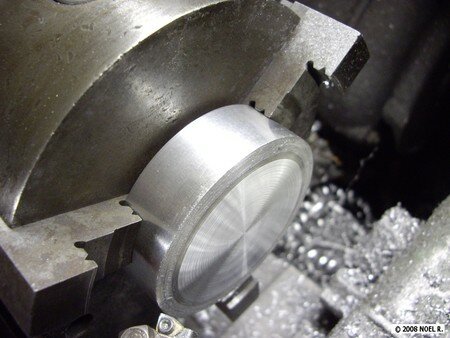
Reprise et dressage de la face .
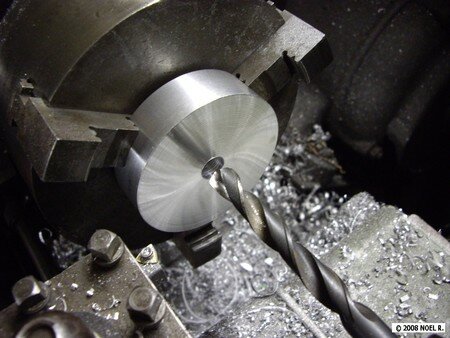
Perçage d'un trou de 13mm .
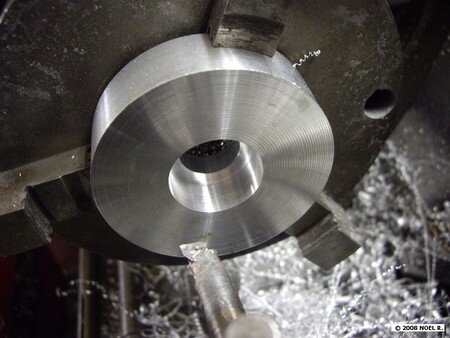
Le trou est alésé à un diamètre de 22 mm pour le passage de l'arbre moteur puis à 32H7 sur une profondeur de 15 mm pour le logement d'un roulement 6201-2RS .
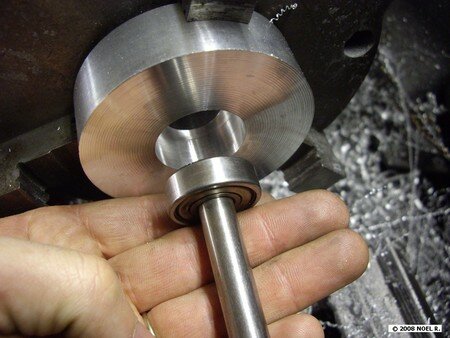
C'est un vieux roulement emmanché sur un axe de 12 mm qui me sert de tampon de contrôle .
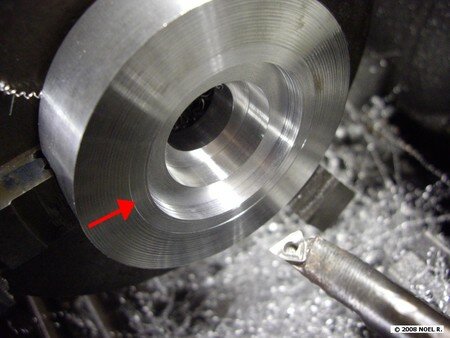
Alésage sur 5 mm de profondeur pour le passage du rotor .Je fais une légère empreinte à un diamètre de 55 mm (flêche rouge) qui me donne facilement la côte de raccordement du rayon de 5 mm que je vais faire par la suite .
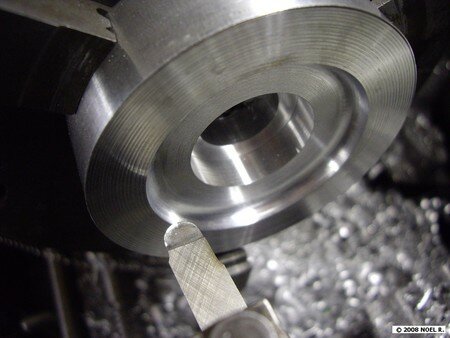
Usinage du rayon à l'outil de forme .
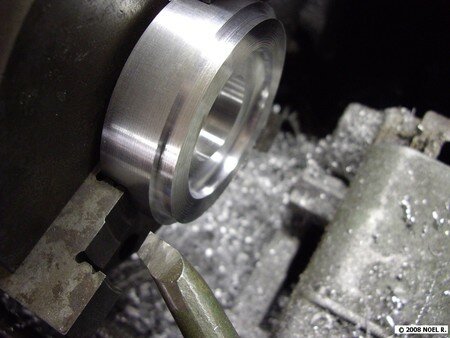
C'est assez atypique mais j'utilise un outil à aléser pour faire l'épaulement qui va s'encastrer dans de bloc moteur . En fait c'est pour passer à l'intérieur des mors .
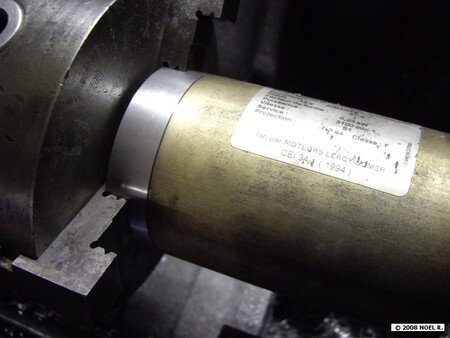
Contrôle de l'ajustage avec le bloc moteur .
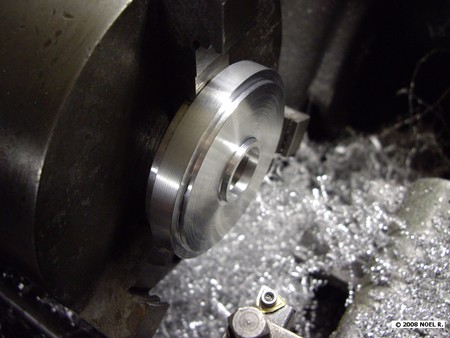
Reprise sur l'épaulement pour usiner la façe avant .
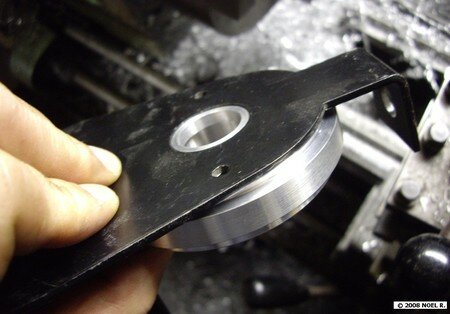
Un ajustage est fait pour maintenir le moteur au bon positionnement d'entraxe des pignons .
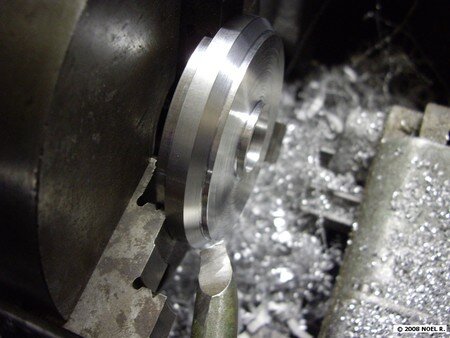
Usinage d'un chanfrein pour laisser passer le débordement du couvercle du réducteur .
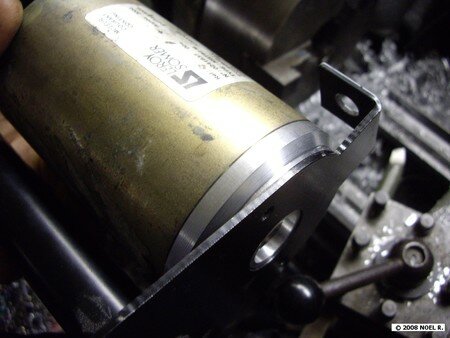
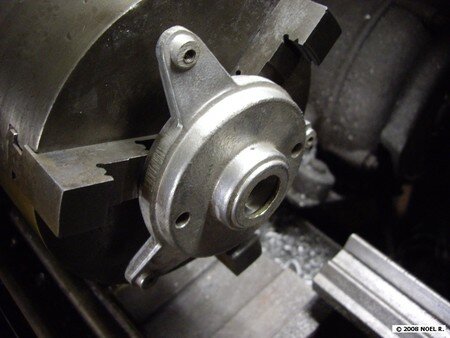
J'utilise le flasque d'origine pour faire un gabarit de perçage des trous pour les tirants .
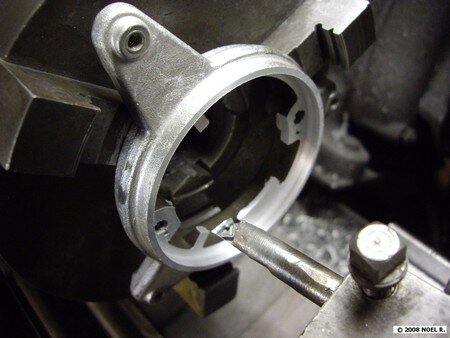
Alésage de ce flasque au diamètre de l'épaulement du nouveau flaque.
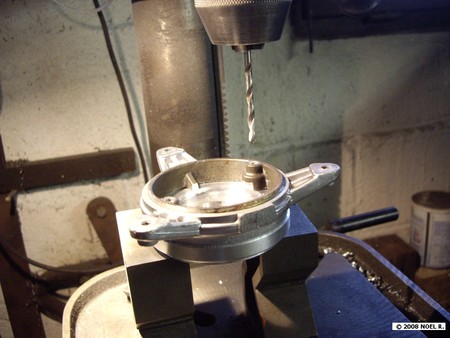
Le gabarit est encastré sur le nouveau flasque pour y pointer les trous des taraudages M5 avec un forêt de 4,2 mm.
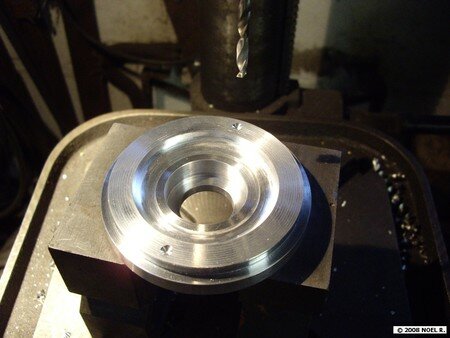
On peut maintenant percer et tarauder les trous .
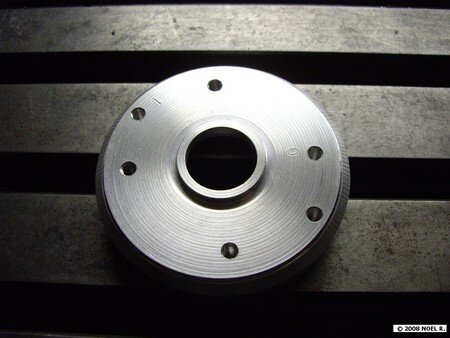
Quatre autres trous M5 sont percés pour la fixation du moteur sur la corps du réducteur .
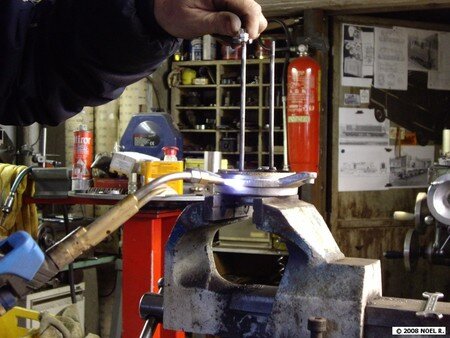
Récupération des tirants en chauffant la pièce pour ramolir le frein-fillet.

Le filetage est brossé pour retirer les résidus de colle .
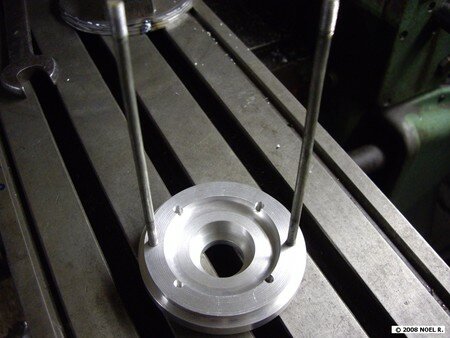
Les tirants sont collés dans le nouveux flasque avant .
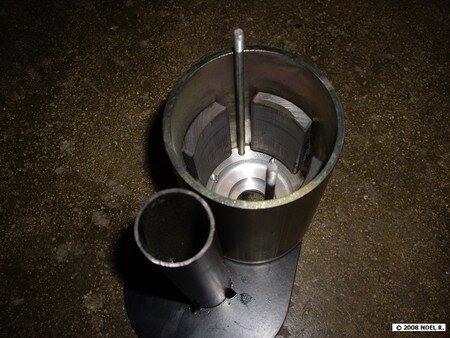
Repérage angulaire de la position des tirants par rapport aux aimants du stator .
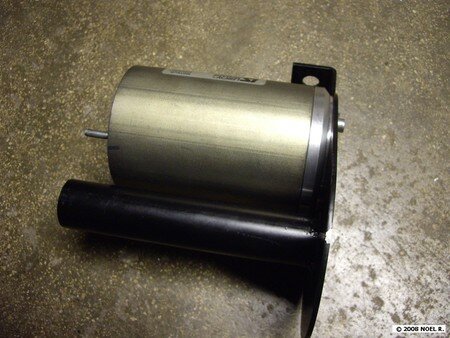
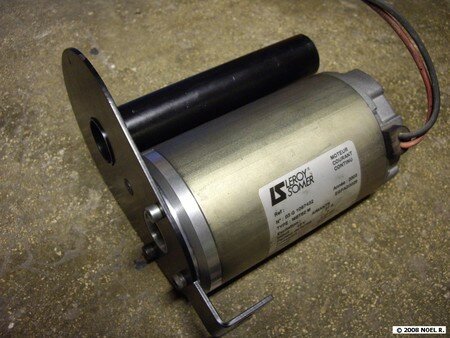
Montage à vide sans le rotor pour voir si tout se monte bien .
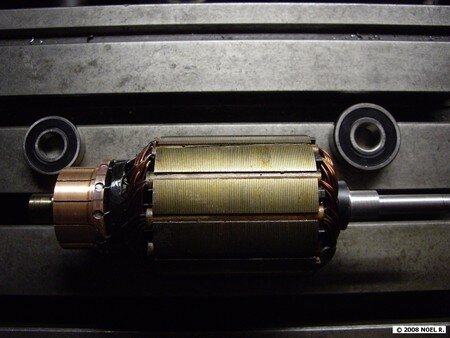
Les roulement tout neufs et étanches vont prendre place sur le rotor . Ils sont montés en utilisant la contre-poupée du tour comme presse et sont collés au scelleroulement.
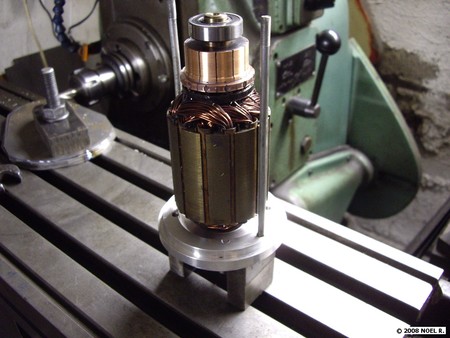
Une fois les roulements montés sur le rotor je colle le roulement avant dans le flasque en laissant polymériser en position verticale .
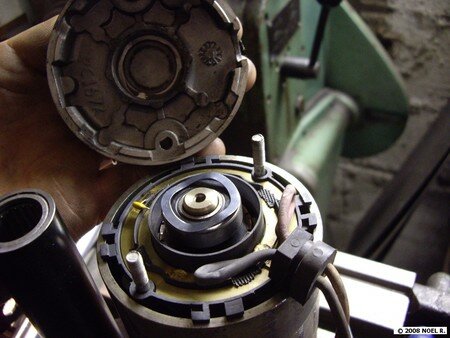
Pour le remontage du moteur je monte le stator sur le flasque avant puis je place le support charbons , la rondelle ondulée est posée sur le roulement arrière et on ferme le tout avec le flasque arrière .
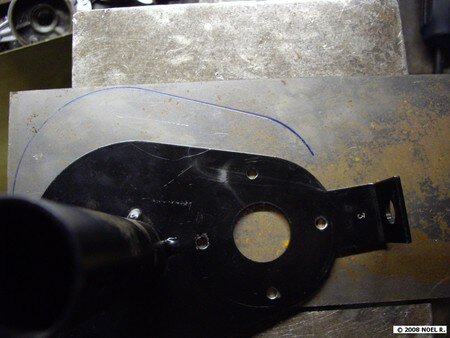
Les couvercles du réducteur sont fait dans de la tôle de 2 mm .Tout d'abord je traces le contour au feutre .
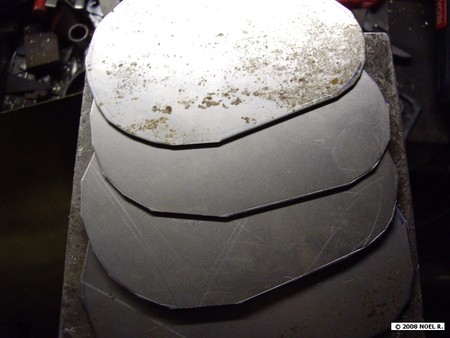
Puis les débits sont cisaillés en laissant un peu de matière en plus par rapport au tracé.
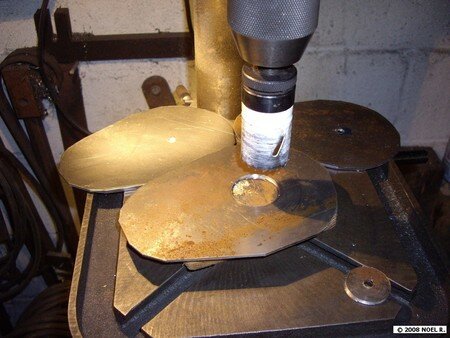
Un trou de 35 mm est fait au trépan.
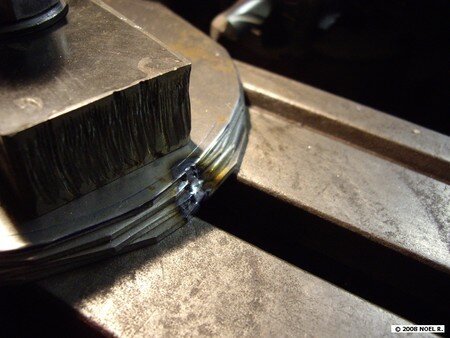
Les pièces sont soudées en paquet aux deux extrémités .
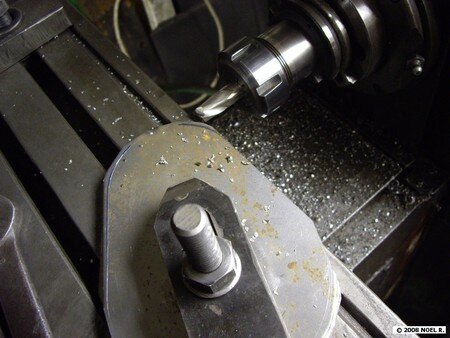
J'ai fais un tracé précis du contour à la pointe à tracer en utilisant le corps du réducteur comme modèle et le fraisage est réalisé en suivant ce trai .Les arondis sont fait par facette succésives de plus en plus fines pour avoir le moins de matière à poncer pour finir la forme .

Ponçage du profil final au lapidaire . Il reste toujours les deux points d'attache.
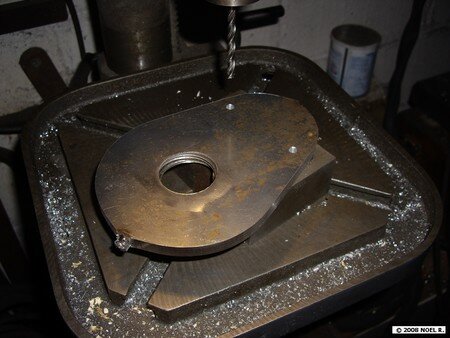
Perçage des deux trous de 5 mm qui serviront à fixer le couvercle .
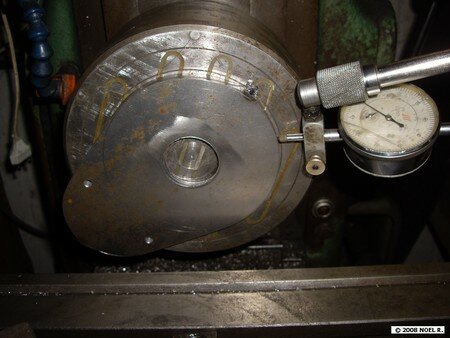
Réglage de la concentricité de la pièce sur le mandrin magnétique pour calibrer l'alésage à un diamètre de 40 mm .
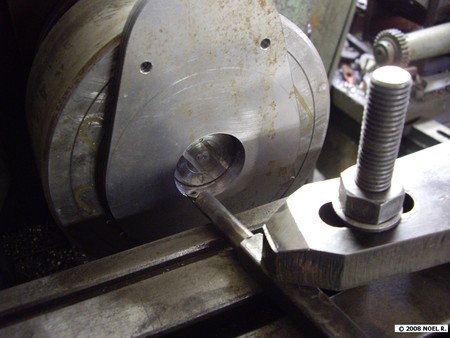
Je prends des petites passes pour ne pas faire glisser la pièce .
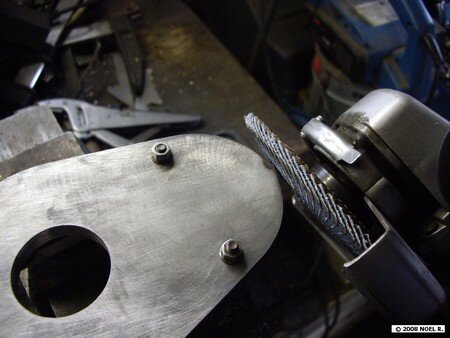
Deux vis sont serrées dans les trous de 5 mm et elles vont prendre le relais pour bloquer le paquet pendant que je meule les points d'attache .
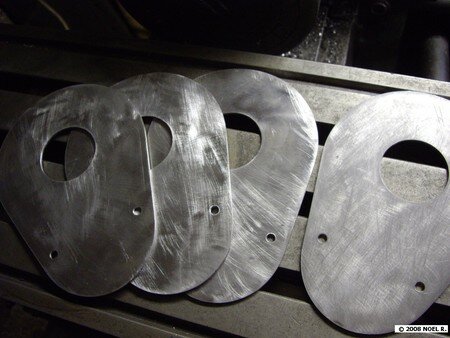
Les quatre flancs sont séparés .
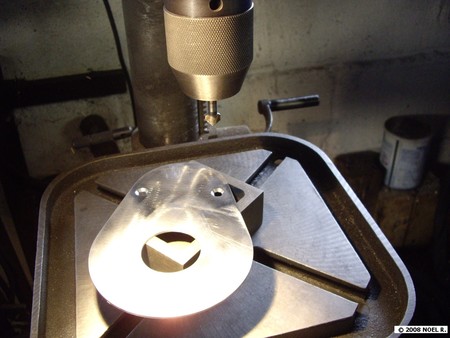
Fraisurage des trous de fixation .
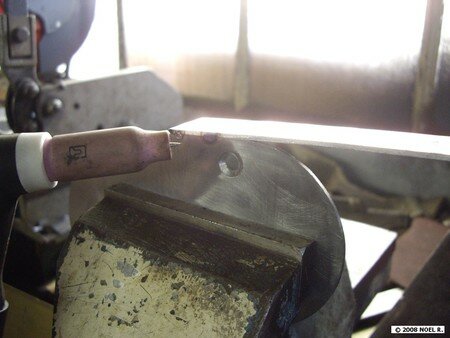
Un fer plat de 2mm est soudé sur le contour et il est mis en forme au fur et à mesure que je le pointe .
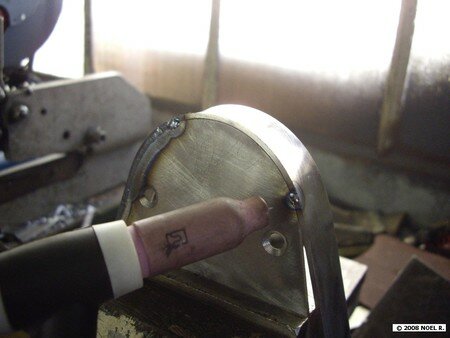
Dans l'ordre des opérations : on cintre , on pointe puis on soude en repartant en arrière.
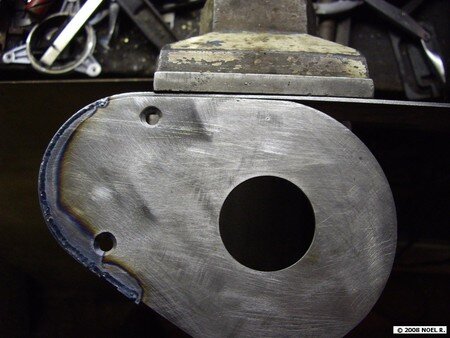
La partie droite est maintenue dans l'étau .
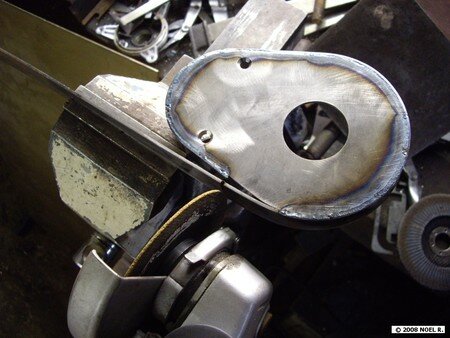
A la fin du contour on donne un coups de meule pour couper le plat à la bonne longueur .
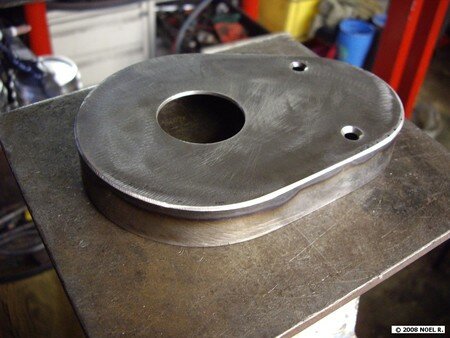
Un léger ponçage est réalisé au disque à lamelles pour retirer les aspérités de la soudure et un cassage de l'angle est fait .
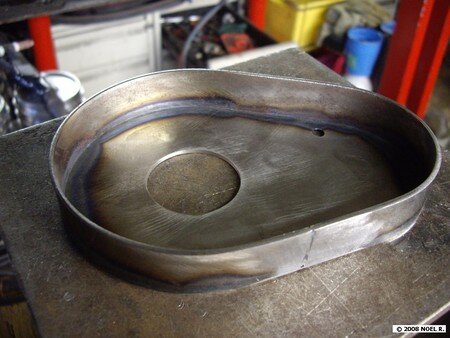
On peut voir à l'intérieur du couvercle que la zone d'affectation thermique est très faible au TIG ce qui entraîne très peu de déformation de la pièce finie.
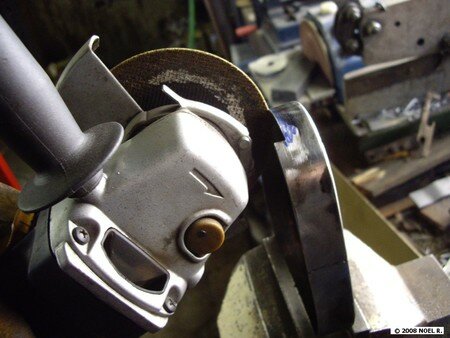
Une encoche est meulée pour laisser passer le bras de rappel du réducteur .
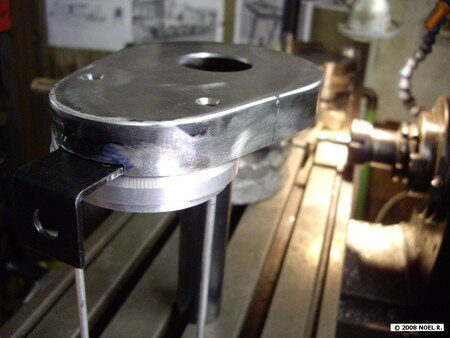
Vérification de l'ajustage .
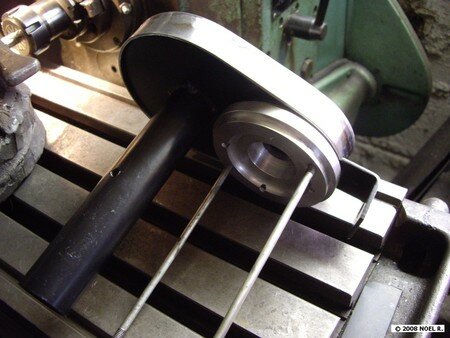
Il aura quand même fallu quelques coups de marteau sur un tas en plomb pour paufiner la forme du couvercle au niveau de l'emboitement sur le corps du réducteur .
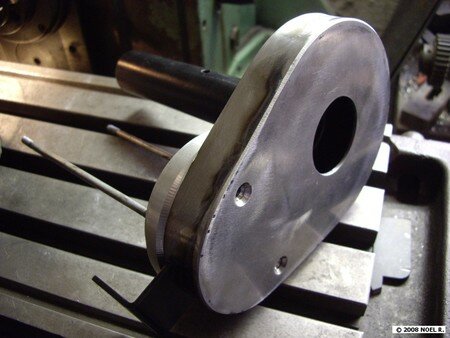
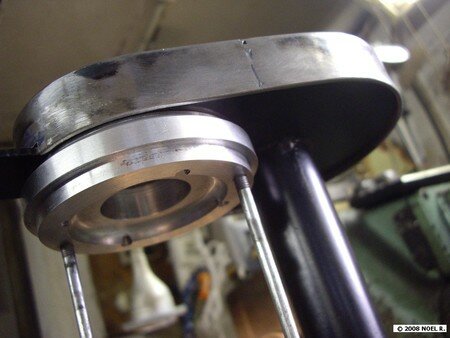
Et voila les couvercles sont finis .
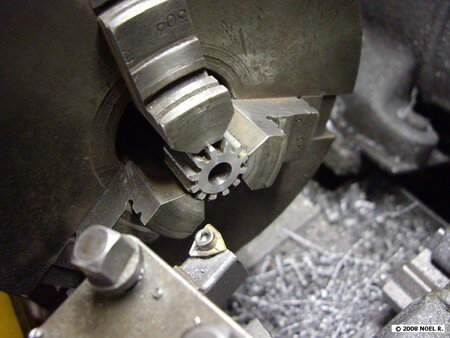
Les pignons de 12 dents sont débarassés de leur épaulement .
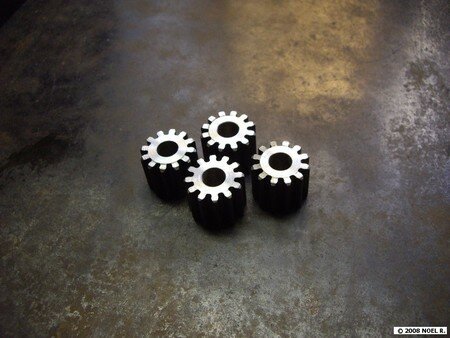
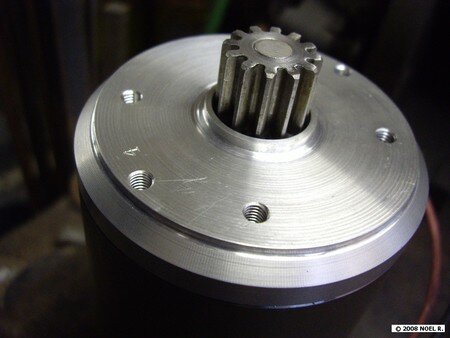
Le pignon est collé au blocpress 638 et l'arbre qui était trop long est coupé au raz après polymérisation .
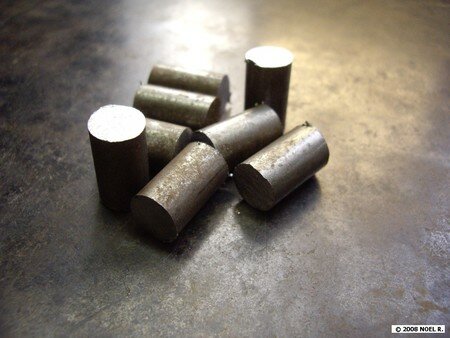
Les entretoises de fixation du couvercle sont faites dans du rond de 12 mm.
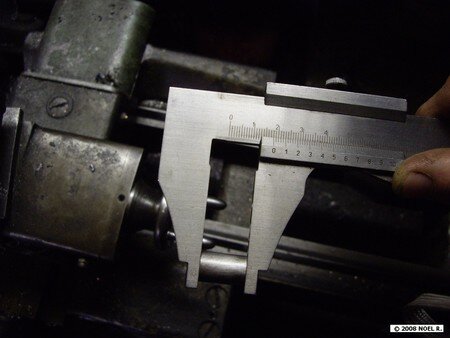
Pour la mise à longueur je dresse les deux faces puis on mesure la côte.
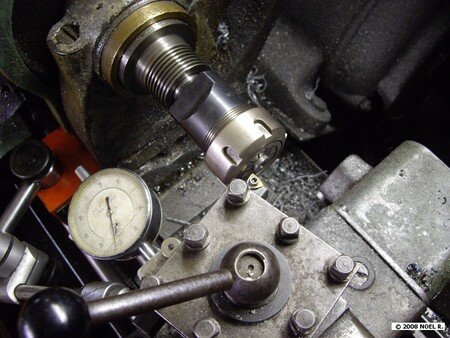
Puis on tangante avec l'outil pour mettre le comparateur à zéro , il reste à usiner la différence de longueur mesurée précédement. Une fois à longueur la pièce est taraudée à M5.
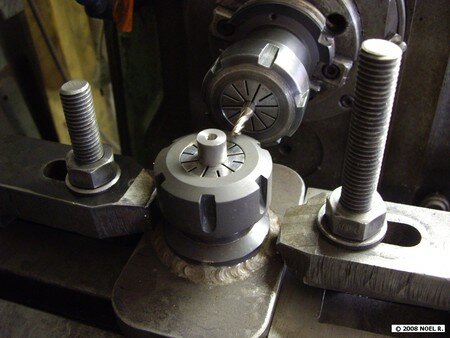
Fraisage de méplats pour le serrage de l'entretoise dans le flasque avant du moteur .
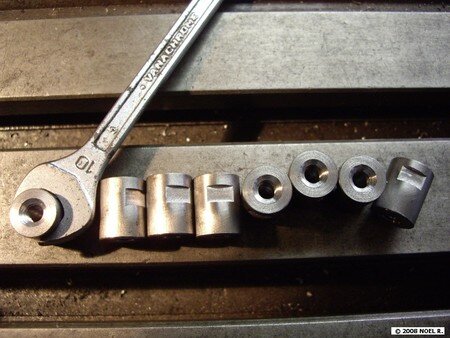
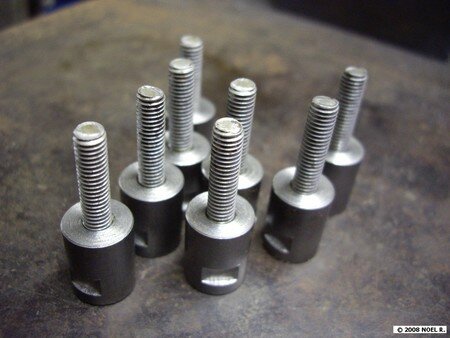
Une tige filetée est collée dans l'entretoise .
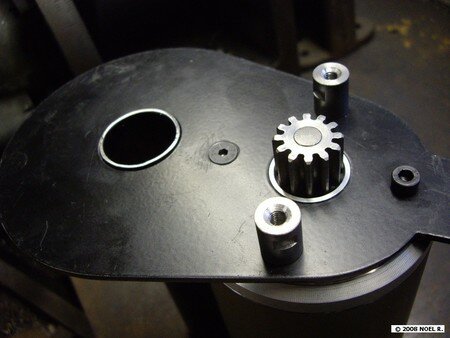

Les entretoises servent aussi au bloquage du moteur .
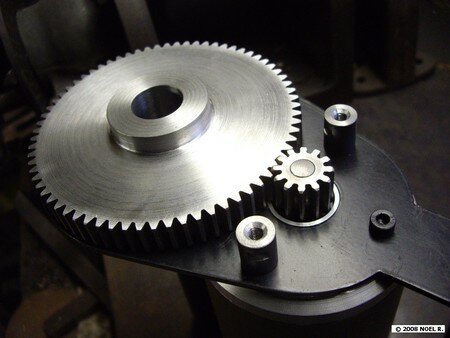

Le couvercle est maintenu par deux vis à tête fraisé .
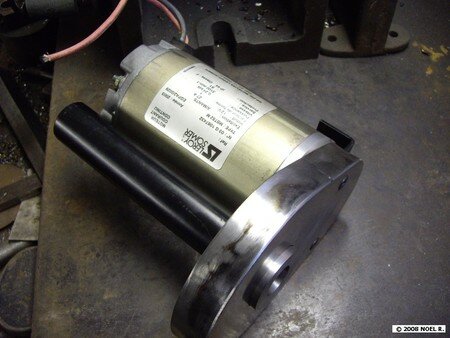
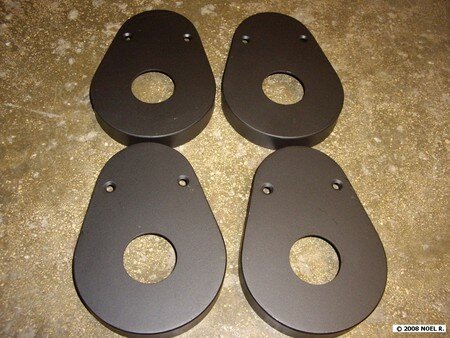
Passage d'un coup de peinture avant montage final .
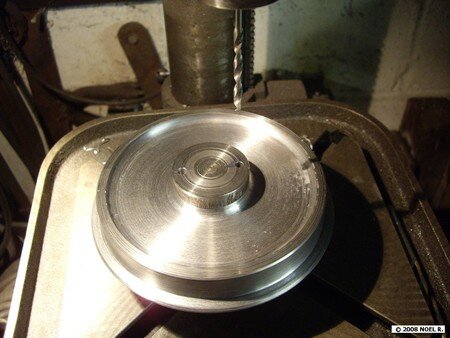
Un gabarit est fait pour le perçage des roues et des pignons .
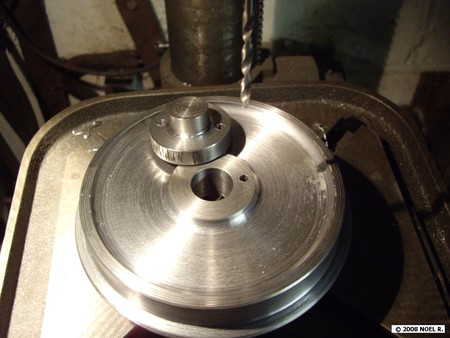
En premier je pointe et je perces à 4,2 mm .
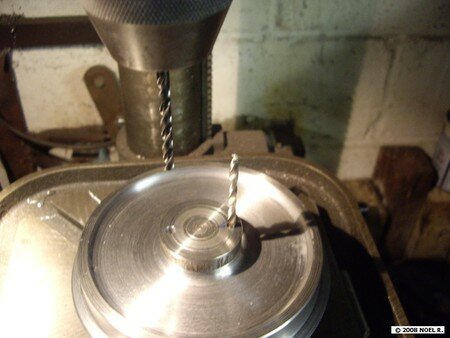
Ensuite le forêt de 4,2 est placé dans le premier trou pour caller le gabarit pendant le perçage du second trou au diamètre 5 mm ensuite le premier trou sera élargi à 5 mm.
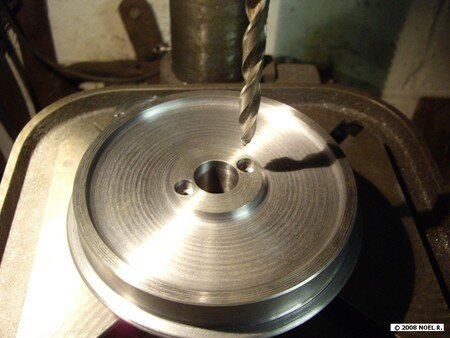
Un lamage est réalisé pour y loger la têtes des vis CHC .
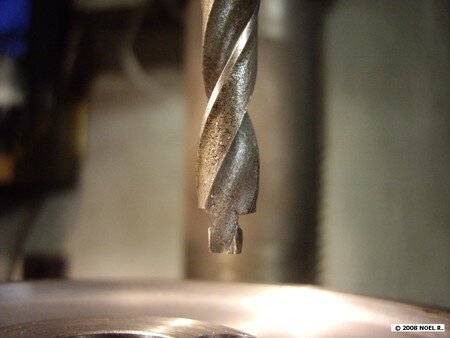
Le forêt à lamer est fabriqué à partir d'un forêt traditionnel qui a subit un nouvel affûtage .
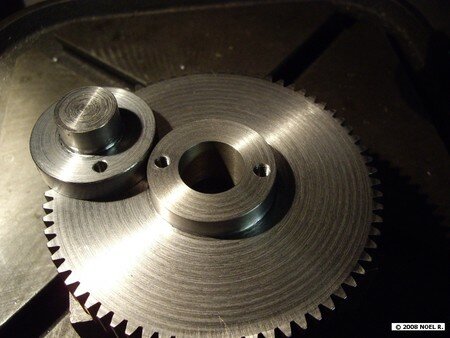
Même principe pour le pignon sauf que lui est taraudé à M5 .
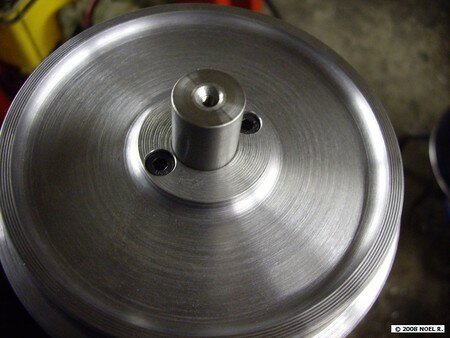
Montage à blanc pour vérifier l'assemblage avant le collage du pignon sur l'arbre .
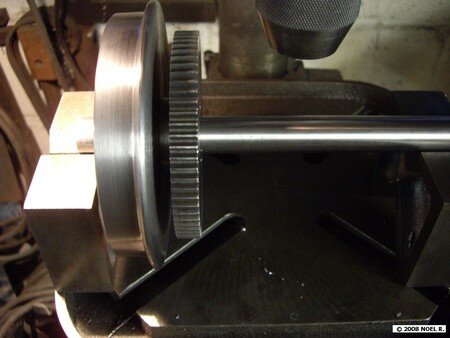
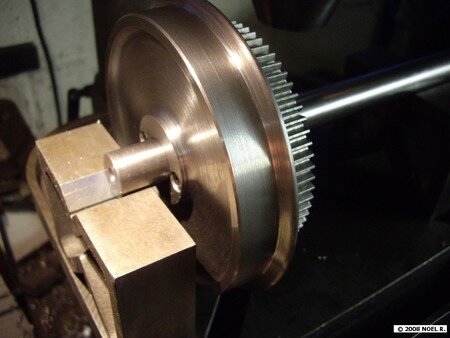
Les têtes de vis sont bien noyées pour ne pas qu'elles frottent sur les boites d'essieux .
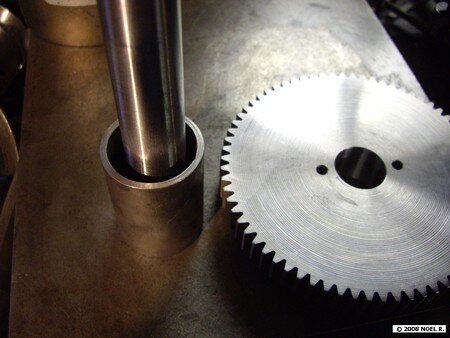
Un tube est tourné à la longueur de la distance entre le bout de l'arbre et le pignon . Les deux faces doivent être bien parallèles pour ne pas que le pignon soit collé de travers .
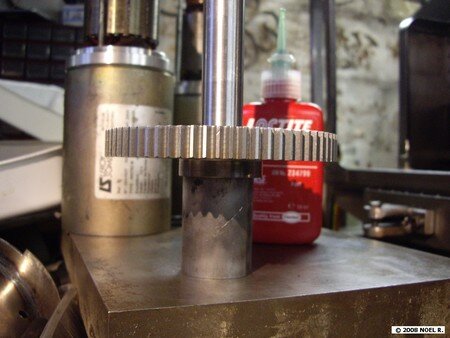
Collage au Loctite 638 .
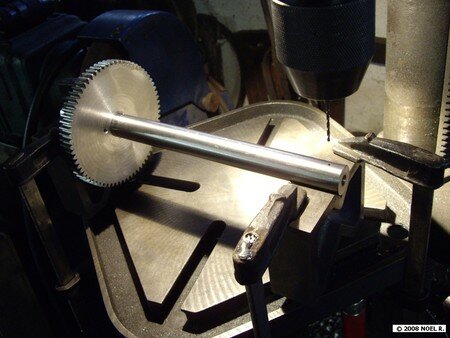
Perçage des trous de 2 mm pour le graissage des cages à aiguilles .
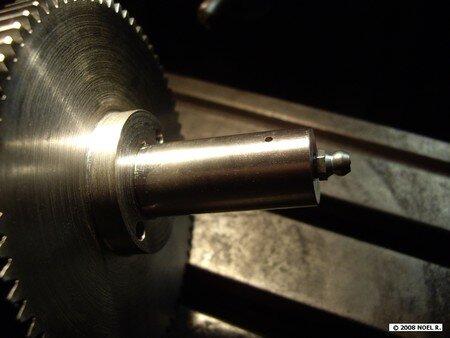
Un graisseur est vissé sur le bout de l'arbre .
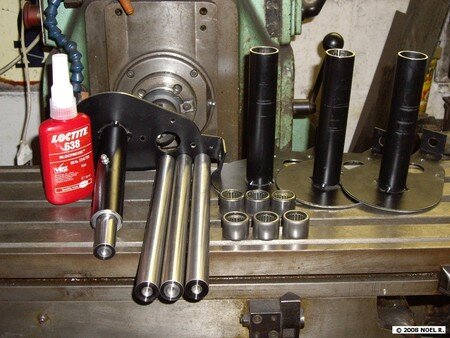
Les cages à aiguilles sont collées dans le tube du corps du réducteur . L'arbre est mis en position pendant la polymérisation de la colle pour garantir le bon alignement des roulements .
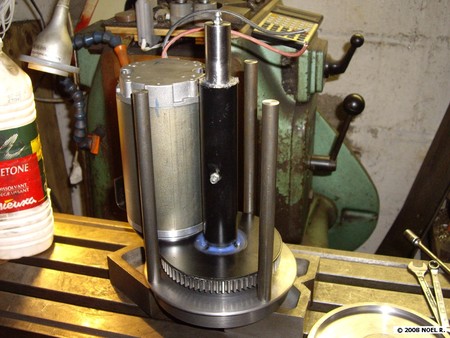
Trois entretoises de 172 mm sont placées entre les deux roues pour un collage au bon entraxe .
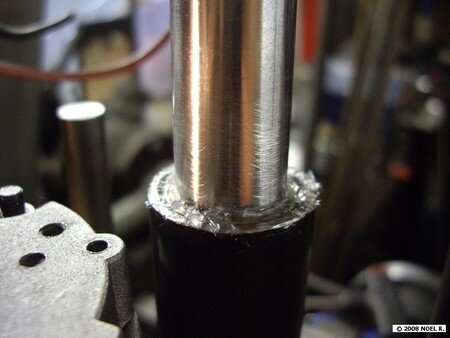
De la graisse est mise sur le joint de la cage à aiguille pour éviter que la loctite ne colle dessus .
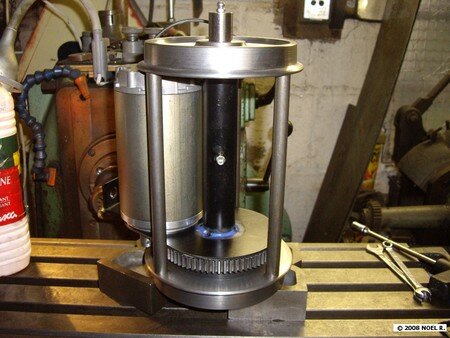
Le lendemain c'est sec et on peut retirer les entretoises pour faire un autre assemblage .
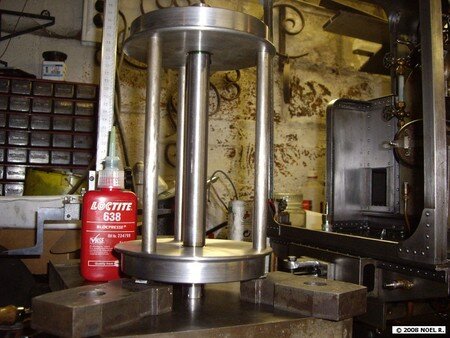
Même principe pour l'essieu porteur .
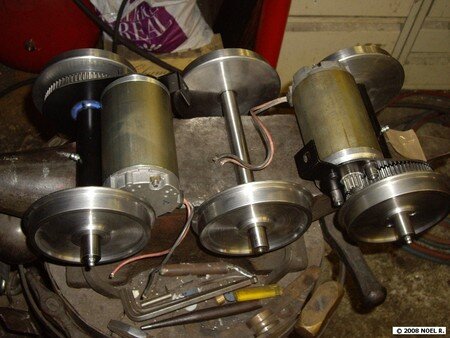
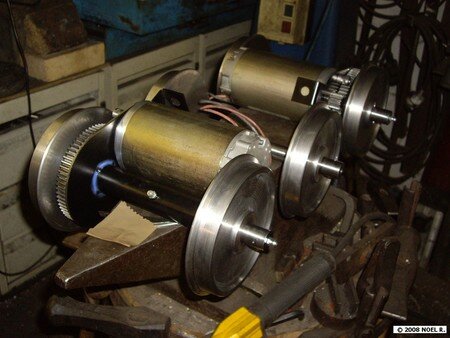
Voila , les six essieux sont collés .
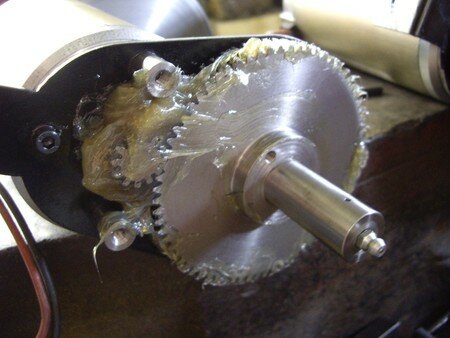
Les pignons sont copieusement enduits de graisse avant de fermer le carter.
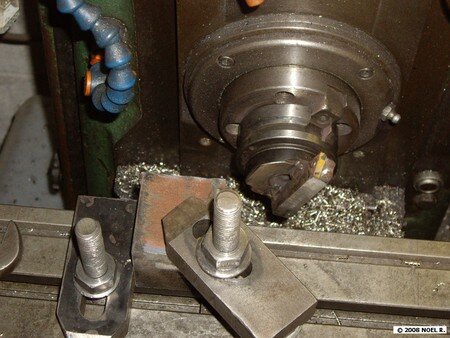
Les boites d'essieux sont faites dans des prismes de 42x45x48 mm .
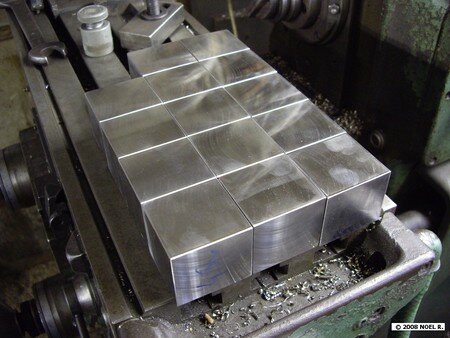
si vous comptez bien il y en a deux de plus au cas où , je ne sais pas encore comment je vais faire la forme extérieur de la boite d'essieu alors je prévois si il y a un raté .
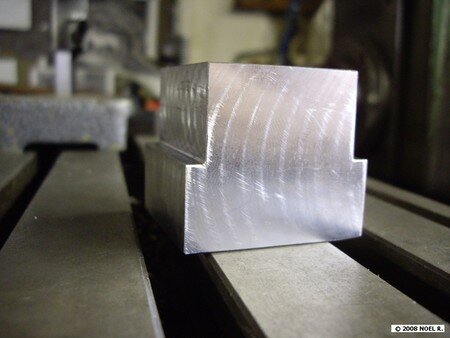
Usinage des épaulement qui vont coulisser dans les glissières du bogie .
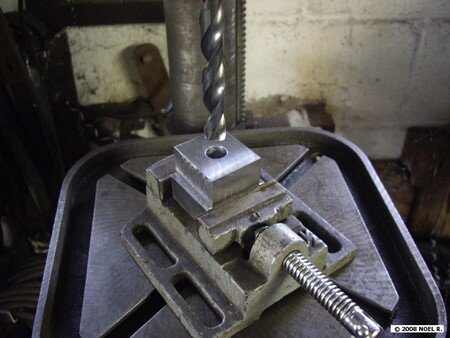
Perçage d'un trou de 14 mm au centre du milieu .
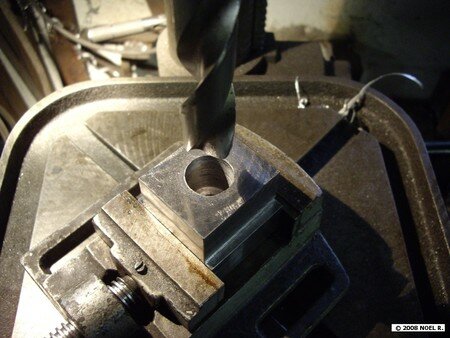
Ce trou est ensuite agrandi à un diamètre de 20 mm sur une profondeur de 26 mm .
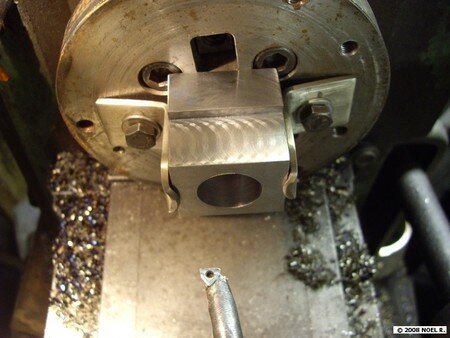
L'alésage qui va recevoir la cage à bille HK 2020 est usiné sur la fraiseuse avec ce montage .
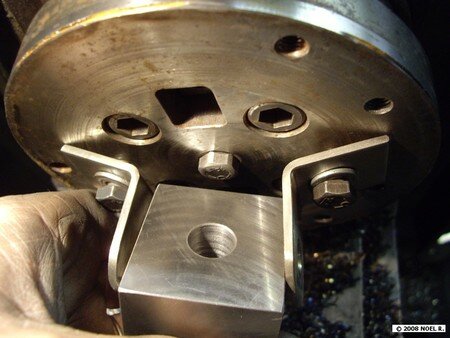
La pièce est centrée sur une vis M8 dont la tête est usinée au diamètre 14 mm in-situ pour garantir la concentricité .
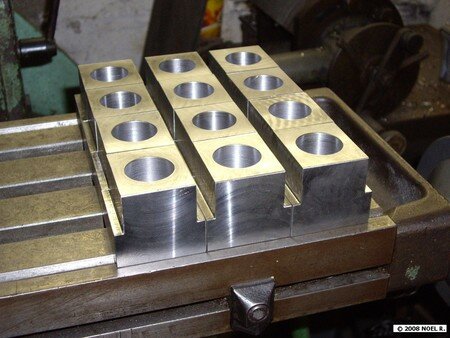
Il n'a pas fallu bien longtemps pour aléser les douze boites d'essieu du fait que les trous étaient bien ébauchés .
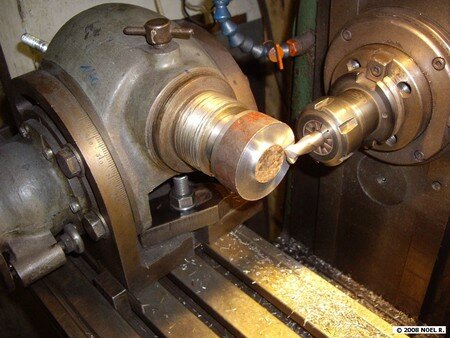
Fabrication d'un montage de reprise avec le diviseur . De cette façon le cimblot de centrage sera bien concentrique .
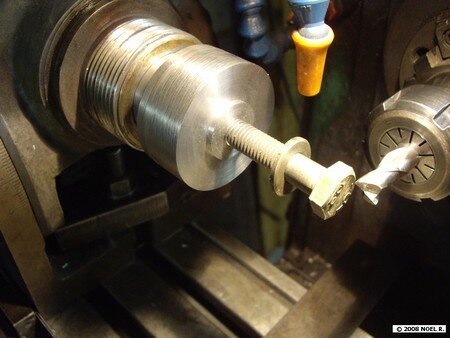
Le montage est taraudé à M12 pour la vis de bridage de la boite d'essieu .
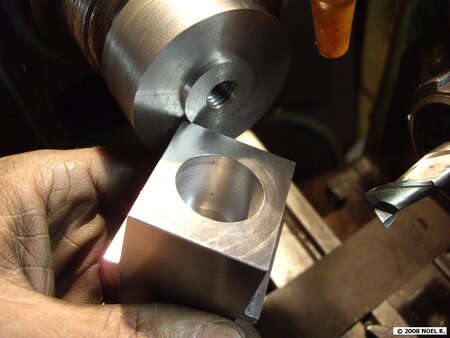
L'alésage de 26 mm s'encastre juste sur le cimblot .
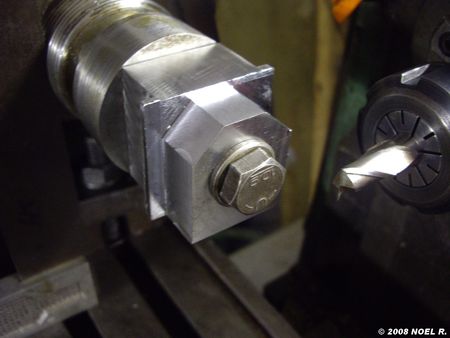
Le devant de la boite d'essieu est ébauchée en facettes .
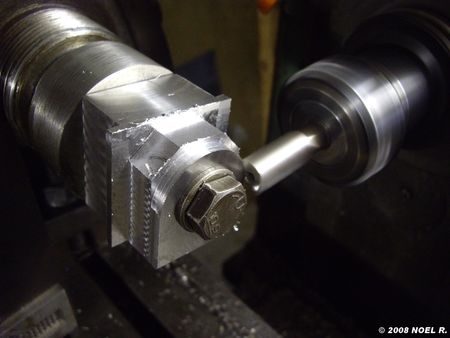
Ensuite viens le travail de forme avec le plateau diviseur .
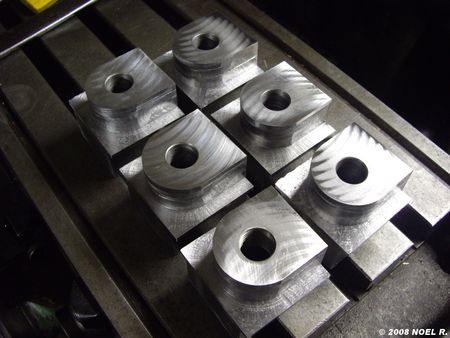
La forme fait 36,5 mm de large .
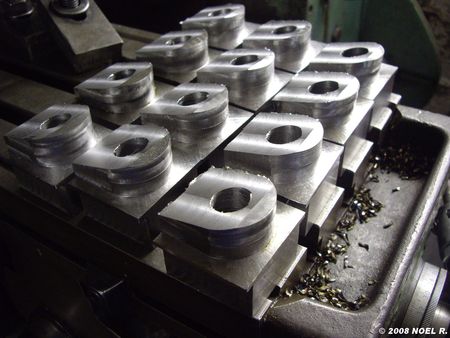
Fraisage de la première pente .
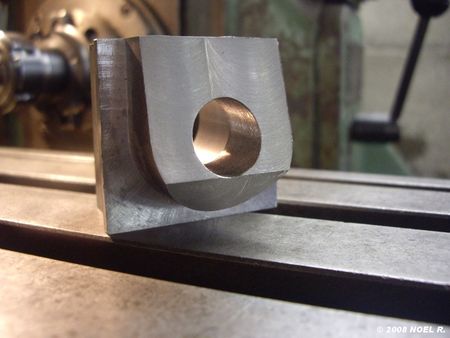
Puis la seconde en bas . Le trou central a été percé au diamètre 17 mm pour faciliter la manipulation de l'enbout de la pompe à graisse .
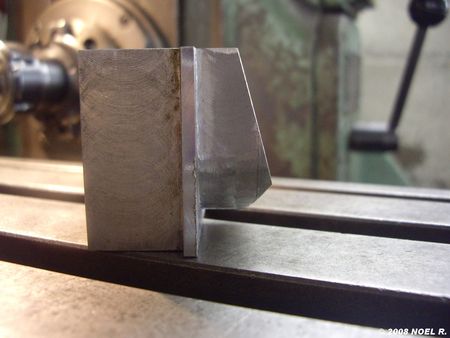
Vue de côté des pentes .
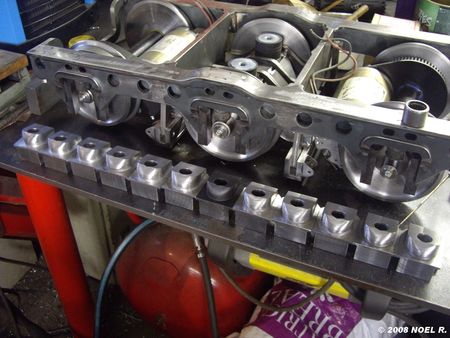
La partie bombée en bas de la boite d'essieu a été finie à la vollée avec la meuleuse , une boite a reçu un coup de peinture noire pour mieux apprécier les formes .
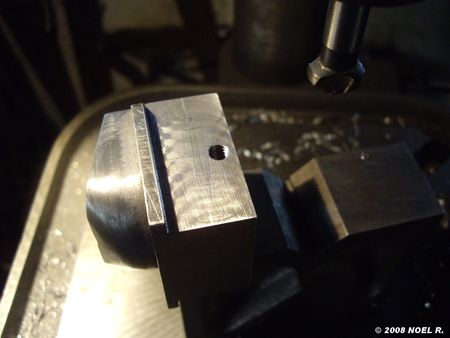
Taraudage M6 sur le côté pour les vis de guidage .
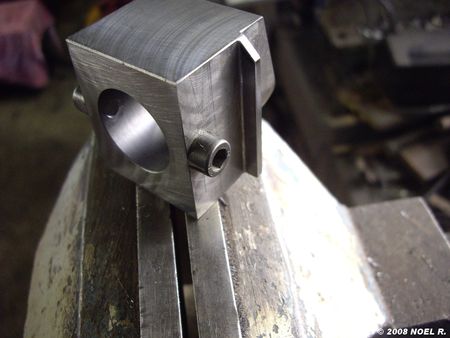
Ces vis sont collées au blocpress .
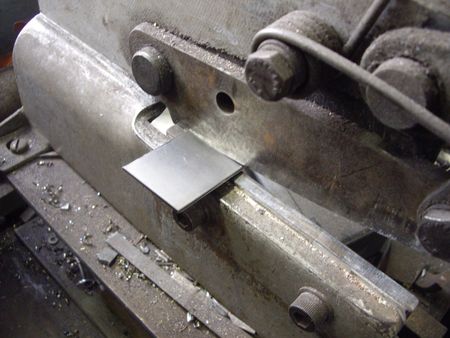
Découpe des flancs dans de la tôle de 2 mm pour faire les couvercles de boite d'essieux. Ils sont prévus avec 1,5 mm de surplus tout autour pour l'usinage .
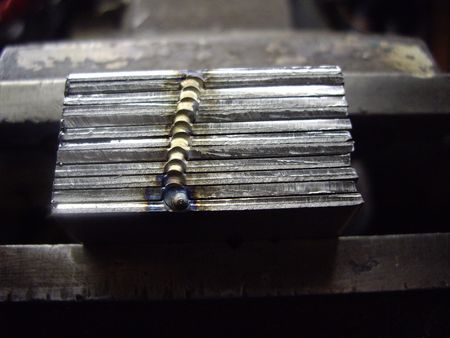
Le bloc est soudé sur trois côtés pour ne pas que cela bouge pendant le fraisage des faces .
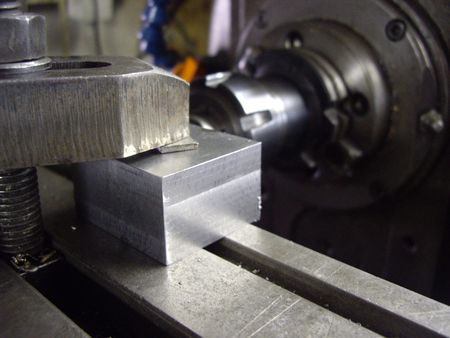
Les trois faces sont dressées et il reste la soudure sur la dernière face qui sera fraisée en forme d'écusson .
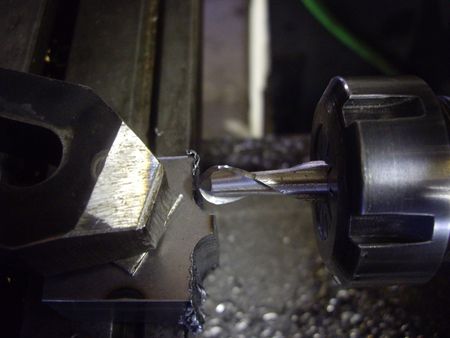
La forme est fraisée avec une fraise à rayon de 5 mm . C'est à ce momment là que la dernière soudure est éliminée , les pièces seront libres après débridage .
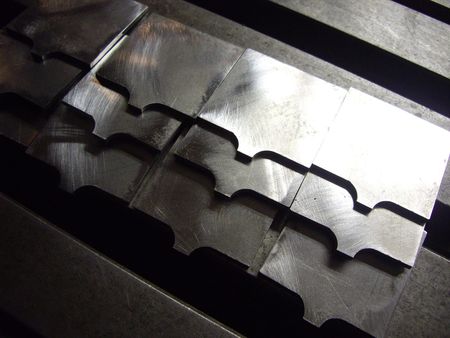
Voila douze couvercles identiques .
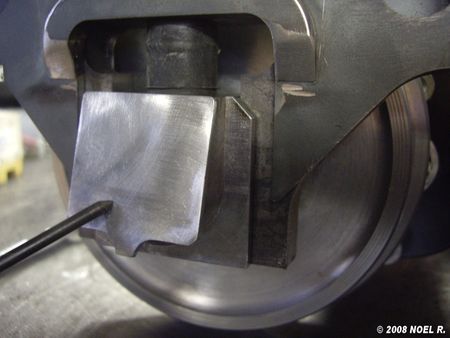
Mise en place pour voir ce que cela donne .
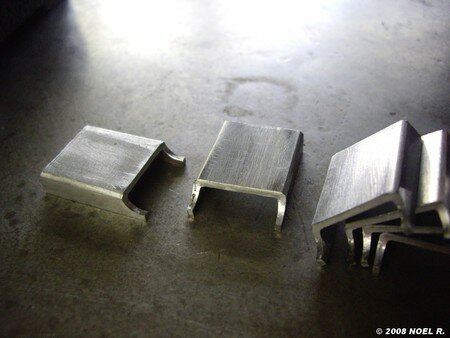
Les charnières des couvercles sont faites dans du tube carré de 20x20 mm qui est découpé à la forme voulue .
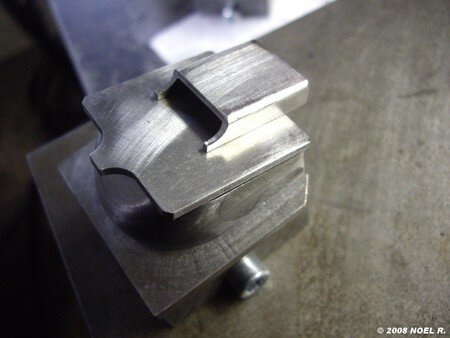
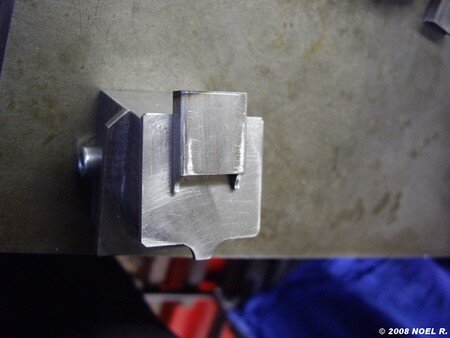
La partie supérieur est plus longue que prévu et sera mise à longueur après soudure .
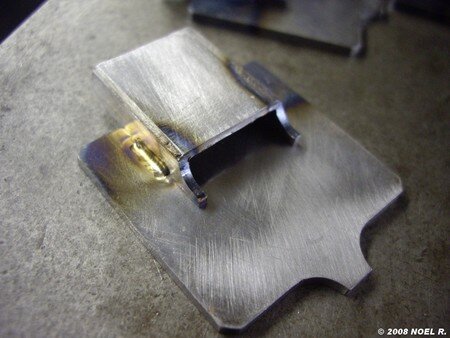
Deux petits cordons au TIG suffisent à assembler les deus pièces .
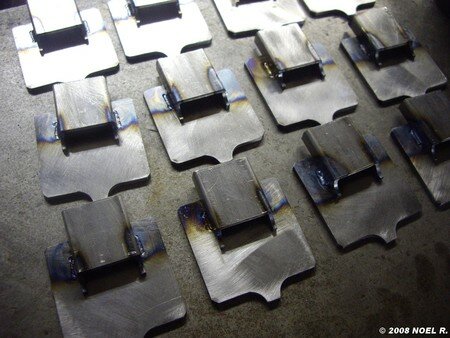
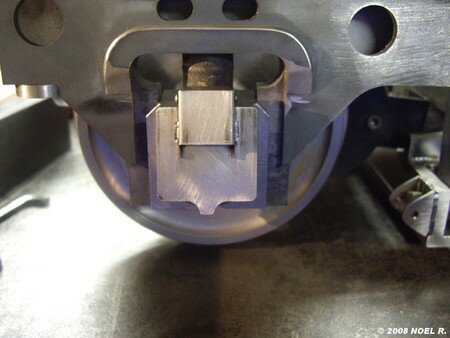
La charnière est percée en haut pour les axes qui sont fait avec des rivets de 2 mm .
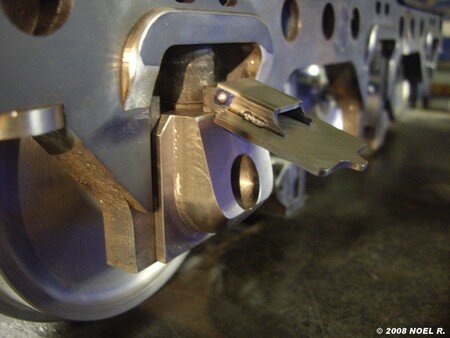
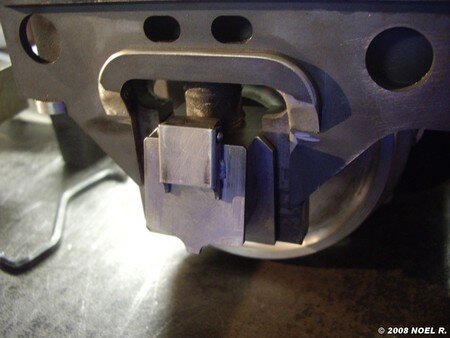
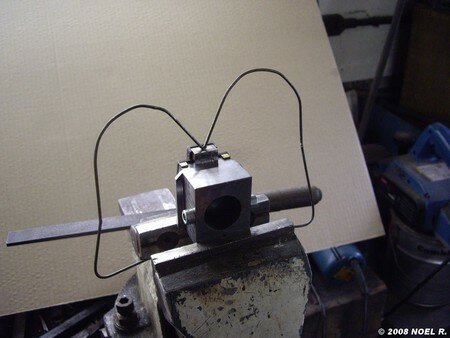
La charnière est faite dans du carré de 8x8 , un morceau de 17 mm de long est maintenu en place par ce fil de fer pendant la soudure .
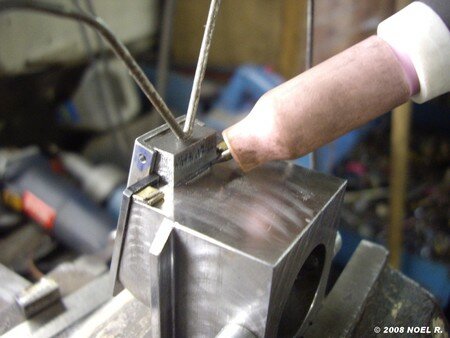
Des petits aimants maintiennent le couvercle à la bonne position pendant la soudure .
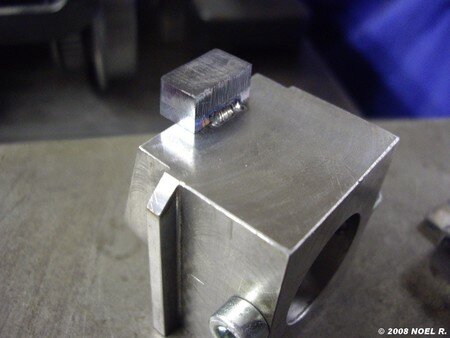
Le cordon est fait dans l'angle sans métal d'apport . Un autre cordon est fait dans l'angle inférieur .
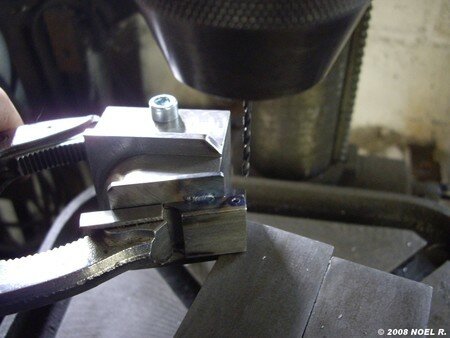
Les trous dans la charnière sont fait par contre-perçage avec le couvercle .
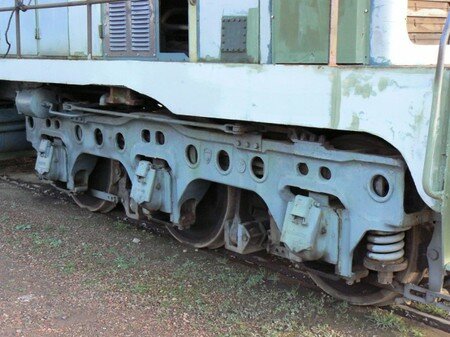
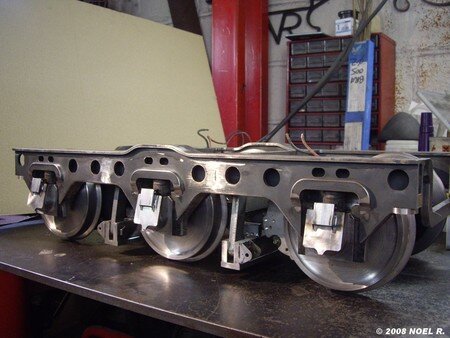
Petit à petit ça commence à ressembler au vrai .
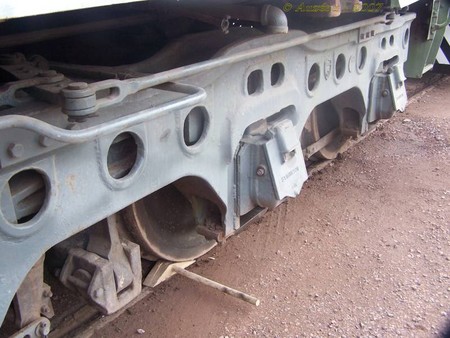
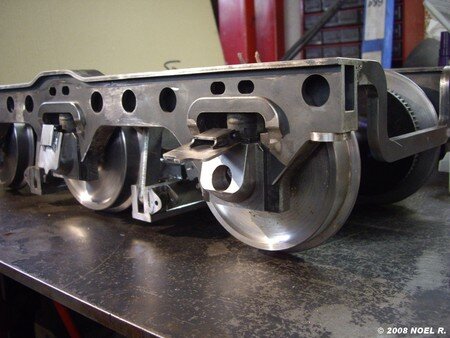
Le couvercle peut être levé pour accéder au graisseur .
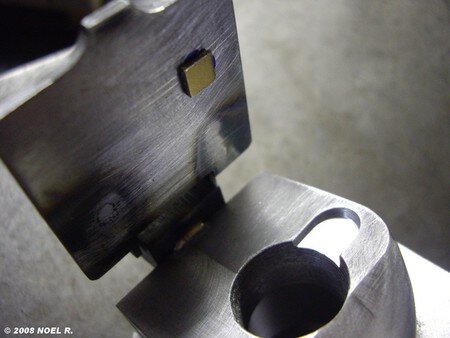
J'ai collé un petit aimant exta puissant pour maintenir le couvercle fermé , c'est comme sur les portes de cuisine !
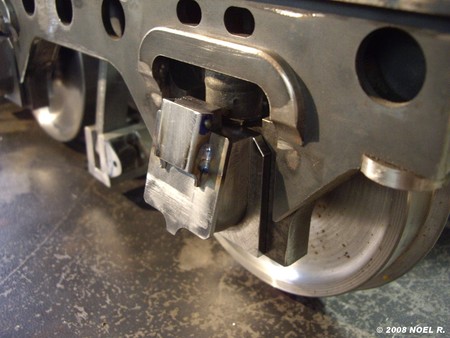
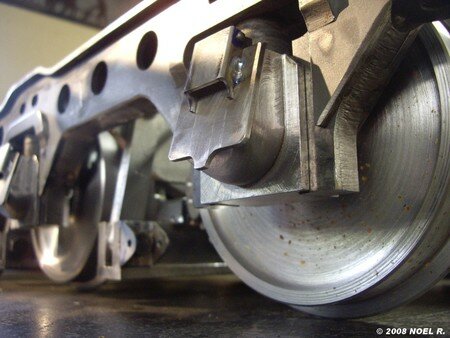

Finalement j'ai réduit un peu la pointe de l'écusson , je le trouve plus joli comme cela .
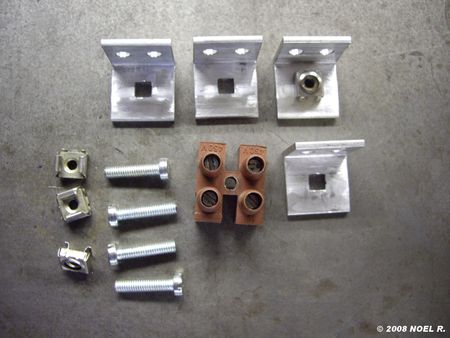
Entre deux je fais des petites modifications au niveau des moteurs , en effet les fils d'alimentation sont trop rigides pour osciller avec le moteur lors de la rotation des bogies dans les courbes , je vais mettre un bornier intermédiaire qui va permettre de repartir en fil plus souple .
Le bornier haute température est fixé sur une équerre en aluminium vissée sur la traverse du bogie.
En attendant le prochain épisode vous pouvez aller faire un tour sur le blogs des copains où vous y trouverez des machine en construction d'une pure beauté.
c'est ici http://ptvbachamois.canalblog.com/ et là http://trainsblayais.canalblog.com/
Je suis à l'atelier en train de faire du copeau .......à suivre .